[ Instrument network instrument research and development ] Biological body is composed of materials, and mechanical properties are the basic performance indicators of materials. Continuously improving mechanical properties to better meet actual application requirements is the common goal of the development of natural and man-made materials, and it is also a common problem they face. In the long-term natural selection and evolution process, the organizational structure and mechanical properties of natural biomaterials have been continuously optimized, allowing organisms to adapt to their living environment, and even achieve the effect of ingenuity. Nature is not only a genius material designer, but also a human teacher. From the perspective of materials science and mechanics, it reveals the organization structure of typical biomaterials in nature and the key mechanism that gives them excellent performance. Refining the design principles of commonality between natural and man-made materials can provide valuable inspiration for the development of high-performance man-made materials.
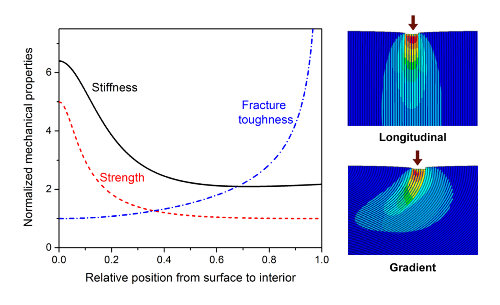
Recently, Liu Zengqian, researcher and Zhang Zhefeng, researcher of the Materials Fatigue and Fracture Laboratory of the Institute of Metal Research, Chinese Academy of Sciences, have cooperated with UC Berkeley, UC Riverside, UC San Diego, Purdue University, etc. Based on systematic research on the structure, mechanical properties and damage mechanisms of typical biomaterials, several common principles for the optimal design of natural and man-made materials have been extracted, including: gradient structure orientation effect, in-situ structure reorientation effect, and multilevel "Suture" interface effects. They revealed the inherent mechanical principles of the above design principles, and further proposed a series of new mechanical theories, providing theoretical guidance for the design and development of new high-performance bionic materials.
Gradient structure orientation effect: Aiming at the changes in the orientation of the macrostructure and microstructure of different biomaterials, they first proposed the concept and design principles of a new type of material structural orientation gradient (Gradient Structural Orientation), and established a gradient structure from the perspective of material mechanics. A series of quantitative relationships between orientation and stiffness, strength, and fracture toughness, for example, Young's modulus and orientation angle have the following quantitative relationships.
On this basis, they clarified the mechanical principle of the gradient structure orientation effect to optimize the performance, and refined a new idea of ​​bionic design to improve the material's ability to resist contact damage. Research shows that as the orientation of the microstructure gradually deviates from the direction of the external force, the stiffness and strength of the material gradually decrease from the surface to the inside, and the fracture toughness gradually increases as the crack increasingly deviates from its easy-to-expand I-type stress surface. Large, so as to achieve the effect of rigid surface and internal flexibility, effectively reduce the damage caused by contact stress on the material.
In-situ structural reorientation effect: For the anisotropic tissue structure of natural biomaterials, they first proposed strategies and design principles for comprehensive optimization of mechanical properties of biomaterials through Adaptive Structural Reorientation. The study found that the microstructure of different biological materials such as wood, fish scales, and bones in nature gradually shifts to an external force under tension, and gradually deviates from the external force under compression. This structural reorientation effect is not only conducive to improving the deformation ability of the material, but also can bring about a comprehensive and simultaneous improvement of different mechanical properties. Under tensile conditions, the reduction of the angle between the reinforcing phase and the stress axis is conducive to improving the stiffness and strength of the material. At the same time, the propagation path of the crack gradually deviates from its maximum normal stress plane, which makes the fracture toughness of the material synchronized Under compressive conditions, the axial partial stress on the reinforcing phase decreases as the orientation gradually deviates from the external force, and the lateral restraint effect on it is strengthened, which is not only conducive to improving the material's resistance to micro-local instability and The mechanical stability of the overall structure is unstable, and it gives the material excellent splitting toughness. They further established a quantitative relationship between different mechanical properties and structural reorientation. For example, the splitting toughness and compressive strain of a material have the following quantitative relationship.
Therefore, biomaterials can use the in-situ structural reorientation effect to comprehensively improve their stiffness, strength, mechanical stability and fracture toughness under different stress conditions, thereby overcoming the contradictory constraints of these properties that are common in traditional material design.
Multi-level "suture" interface effect: Aiming at the constantly changing micro-orientation of the widely varying micro-orientation in skulls, fish scales, pangolin scales and other biomaterials, the zigzag multi-level "suture" interface structure (Hierarchical Suture Interface) was established from the perspective of fracture mechanics The basic criteria for judging the interaction mode of cracks and interfaces and the path of crack propagation were proposed. For the first time, a new viewpoint was proposed that a multi-level "stitching" structure could toughen the interface by promoting cracks through the interface, and revealed the "stitching" structure Influence of micro-geometry and structure series on interface toughness and mechanism. The study found that the multi-level "stitching" structure can cause the angle between the crack and the interface to deviate from its initial incident angle, and increase the complexity and ruggedness of the crack's propagation path along the interface, thereby significantly reducing the effective stress intensity that drives the crack to continue to deflect along the interface. factor. For example, the ratio of the effective stress intensity factor at the crack tip that urges a crack through the interface to deflection along the interface is:
The multi-level "stitched" structure makes cracks more inclined to penetrate the interface rather than enter the interface, so it effectively toughens the interface, and the toughening effect of the interface will increase with the sharpness of the sawtooth and the number of structural levels. And significantly enhanced. They further proposed the concept of the characteristic critical stress intensity factor ratio, which can quantitatively reflect the effect of multi-level "stitching" structure on the toughening effect of the interface as well as the interface's geometry and structural order.
The valve stem is an important part of the valve.
It is used to drive, connect the actuating mechanism or handle, and directly
drive the spool to move or rotate, so as to realize the function of valve switch
or regulation.Valve stem in the valve opening and closing process is not only
moving parts, stress components, but also seals. At the same time, it is
subjected to the impact and corrosion of the medium, and it also causes friction
with the packing. Therefore, in selecting the stem material, it must be
guaranteed that it has sufficient strength at the prescribed temperature, good
impact toughness, scratch resistance, corrosion resistance. The valve stem is a
vulnerable part, and the mechanical performance and heat treatment performance
of the material should be paid attention to when selecting.The valve stem in the
valve opening and closing process, under tension, compression and torsion force,
and direct contact with the media, as well as the relative motion between the
friction and filler, so in the choice of stem material, must ensure that it
provides adequate temperature strength, good impact toughness, abrasion
resistance and corrosion resistance of.
Marine Valve Parts
Marine Valve Parts,Steel Marine Valve Parts,Marine Valves,Marine Ball Valves,Marine Spare Parts
ZhouShan HeCheng Machinery Co., LTD. , http://www.hcmarineparts.com